Blog detail
What are the differences between the production process of transparent FR-4 circuit boards and ordinary FR-4 circuit boards?
Release time:
2025-07-26 13:20
What are the differences between the production process of transparent FR-4 circuit boards and ordinary FR-4 circuit boards?
There are differences between transparent FR-4 circuit boards and ordinary FR-4 circuit boards in terms of core substrate composition and application scenarios, so there are also multiple key differences in production processes, mainly reflected in substrate treatment, process accuracy control, and selection of laminating materials. Here is a specific comparison:
1. Substrate composition and pretreatment process
Ordinary FR-4:
The substrate is made of epoxy resin as the matrix, filled with glass fiber cloth, and added with bromine based flame retardants (such as tetrabromobisphenol A) and dark fillers. The substrate itself is light yellow or brown in color and opaque. Pre treatment mainly focuses on optimizing the adhesion of copper foil, without considering transparency.
Transparent FR-4:
The substrate is made of bromine free transparent epoxy resin (or modified epoxy resin), with finer glass fiber cloth (such as ultrafine glass fiber, diameter 5-8 μ m, ordinary FR-4 is 10-15 μ m), and reduces or removes dark fillers. The substrate transparency is achieved through formula adjustment. Pre treatment requires strict control of resin purity to avoid impurities or bubbles affecting transparency. Some processes may add polishing steps to the substrate surface to reduce scattering.
2. Laminated process and material selection
Ordinary FR-4:
Ordinary semi cured sheets (including epoxy resin and glass fiber) are used for interlayer bonding, and there is no requirement for transparency during lamination. Pressure and temperature parameters are mainly used to ensure bonding strength and dimensional stability, allowing for a small amount of bubbles or uneven resin flow (without affecting functionality).
Transparent FR-4:
Transparent semi cured sheets (made of bromine free transparent resin and ultra-fine glass fibers of the same material as the substrate) should be used between layers to avoid light obstruction caused by interlayer materials.
Accurate control of pressure (usually higher, such as 1.5-2MPa, compared to 1-1.2MPa for ordinary FR-4) and heating rate is required during lamination to reduce the generation of bubbles or ripples caused by resin flow (bubbles can cause light scattering and reduce transparency).
After lamination, defoaming treatment (such as vacuum secondary curing) may be added to further eliminate small bubbles.
3. Circuit pattern transfer and etching process
Ordinary FR-4:
Traditional photolithography (UV exposure+development) can be used, with moderate requirements for edge accuracy of the circuit (such as ± 0.05mm), and the corrosive effect of etching solution (such as ferric chloride) on the substrate can be ignored.
Transparent FR-4:
Due to the transparency of the substrate, the exposure process needs to be more precise: ordinary ultraviolet light may penetrate the substrate and cause backside photosensitivity, requiring the use of laser direct imaging (LDI) technology. High precision laser beams are used to directly image on the copper foil to avoid light transmission interference, and the edge accuracy of the circuit is required to be higher (within ± 0.02mm).
Etching solution needs to be optimized: Transparent resin is more sensitive to strong acidic etching solutions, and low concentration etching solutions (such as acidic copper chloride solution) should be used to shorten the etching time and avoid the substrate surface from being corroded, resulting in a decrease in transmittance.
4. Surface treatment process
Ordinary FR-4:
Surface treatment is mainly aimed at protecting the copper layer and enhancing weldability, such as tin spraying, immersion gold, OSP (organic solder protectant), etc. The coating color does not affect the function (such as immersion gold appearing golden yellow and tin spraying appearing silver white).
Transparent FR-4:
Surface treatment should balance transparency and conductivity:
Priority should be given to transparent conductive coatings (such as ITO film sputtering) or thin high-purity gold deposition (gold layer thickness<0.1 μ m) to avoid traditional thick layer tin spraying or gold deposition blocking light.
In some scenarios, the transparent appearance of the substrate needs to be retained, and even surface treatment can be omitted, with only the etched copper foil directly exposed (the thickness of the copper foil needs to be controlled to avoid excessive thickness affecting light transmission).
5. Quality inspection standards
Ordinary FR-4:
The focus of the inspection is on electrical and mechanical properties such as circuit conductivity, interlayer insulation resistance, and temperature resistance (such as Tg value), and there is no requirement for appearance transparency.
Transparent FR-4:
In addition to routine electrical performance testing, it is necessary to add transparency testing (using a spectrophotometer with a wavelength range of 400-700nm) and optical defect testing (such as inspecting bubbles, glass fiber cloth texture clarity, surface scratches, etc. through a microscope, which can significantly reduce transparency).
Summary: Core Differences Core
The core goal of the transparent FR-4 process is to maintain high transparency while ensuring circuit functionality. Therefore, targeted optimization is required in areas such as substrate purity, lamination accuracy, exposure technology, and surface treatment. The cost and process complexity are higher than those of ordinary FR-4. However, ordinary FR-4 places more emphasis on cost-effectiveness and traditional electrical performance, without considering special controls related to light transmission.
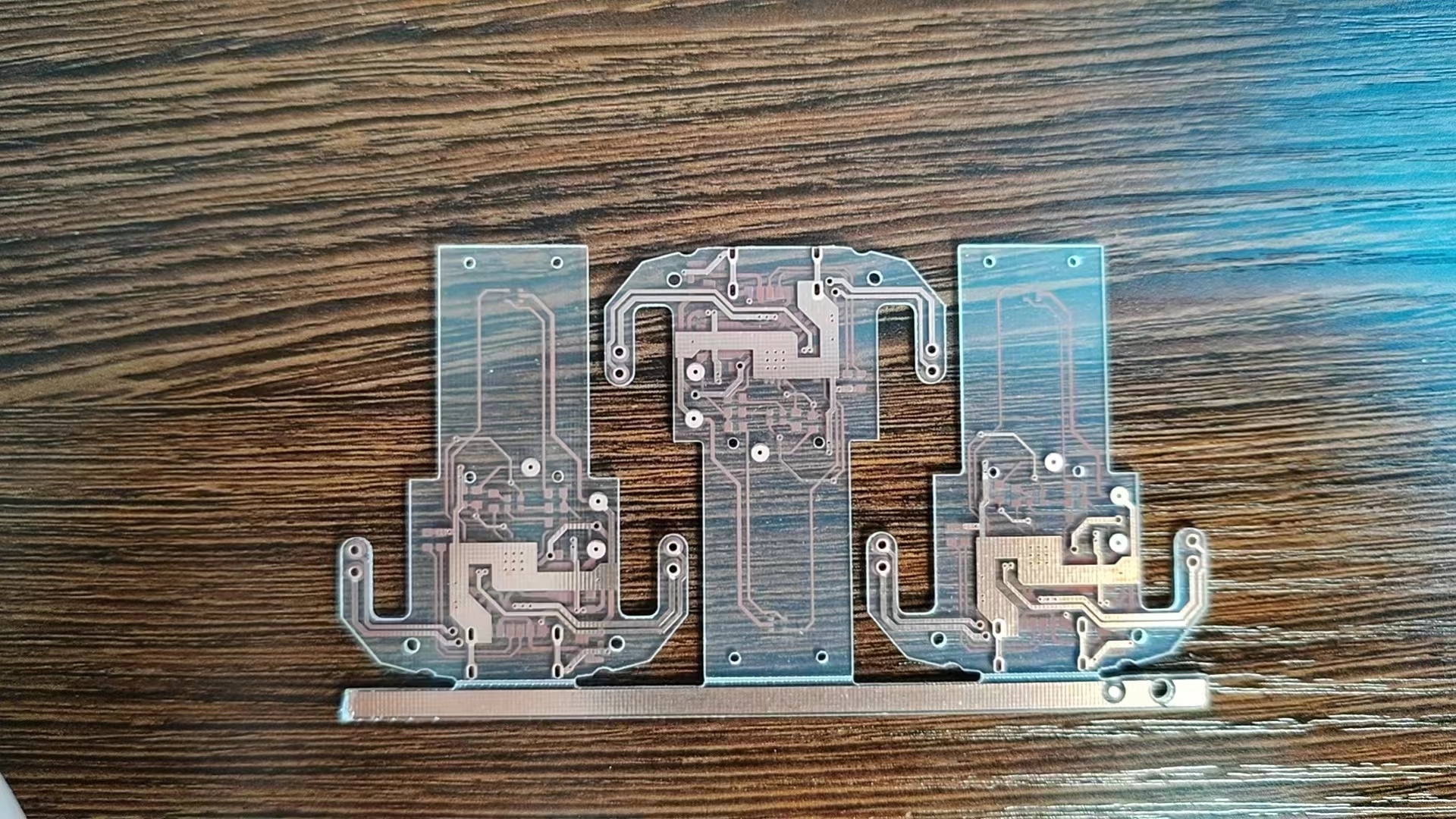
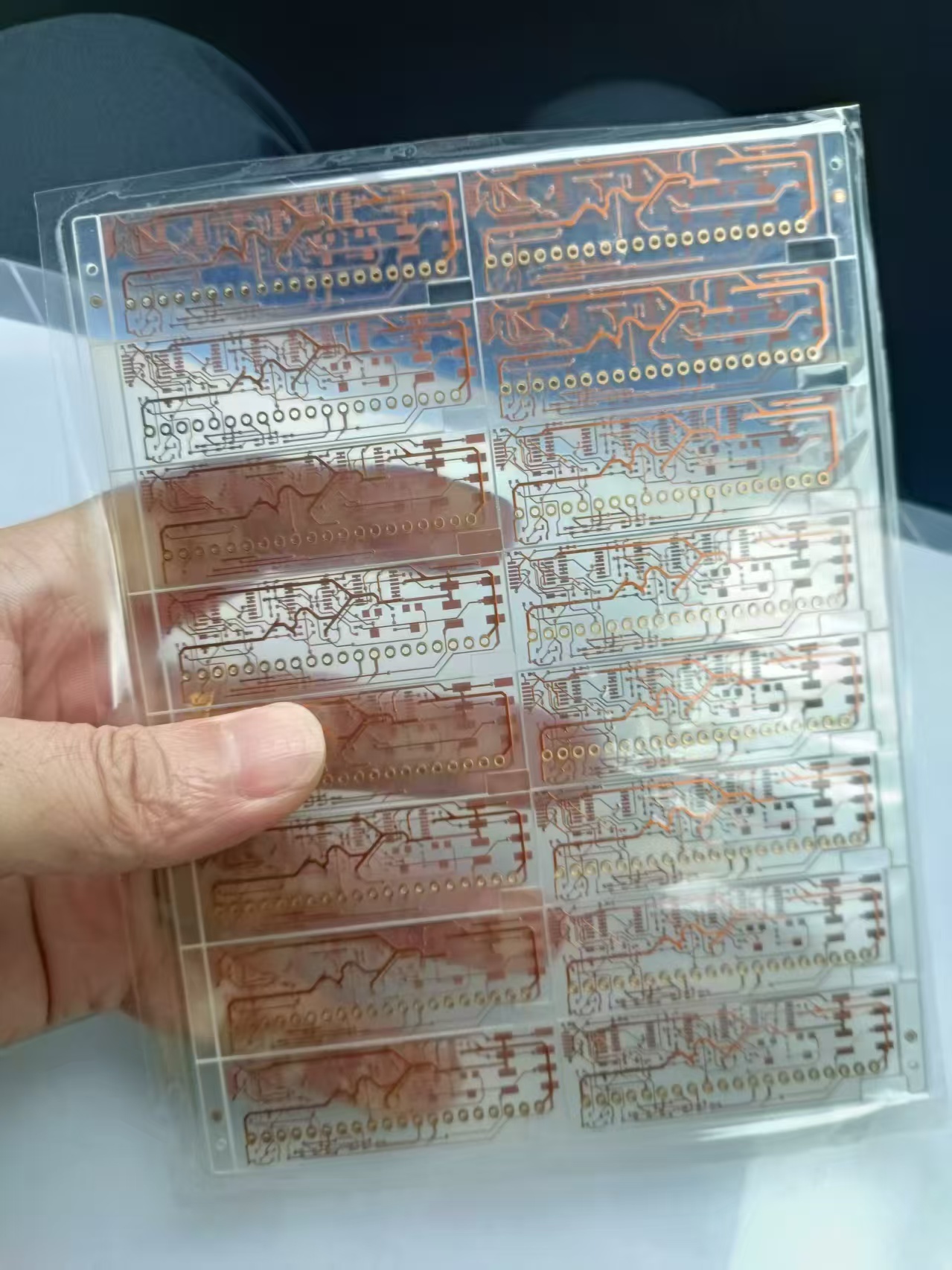
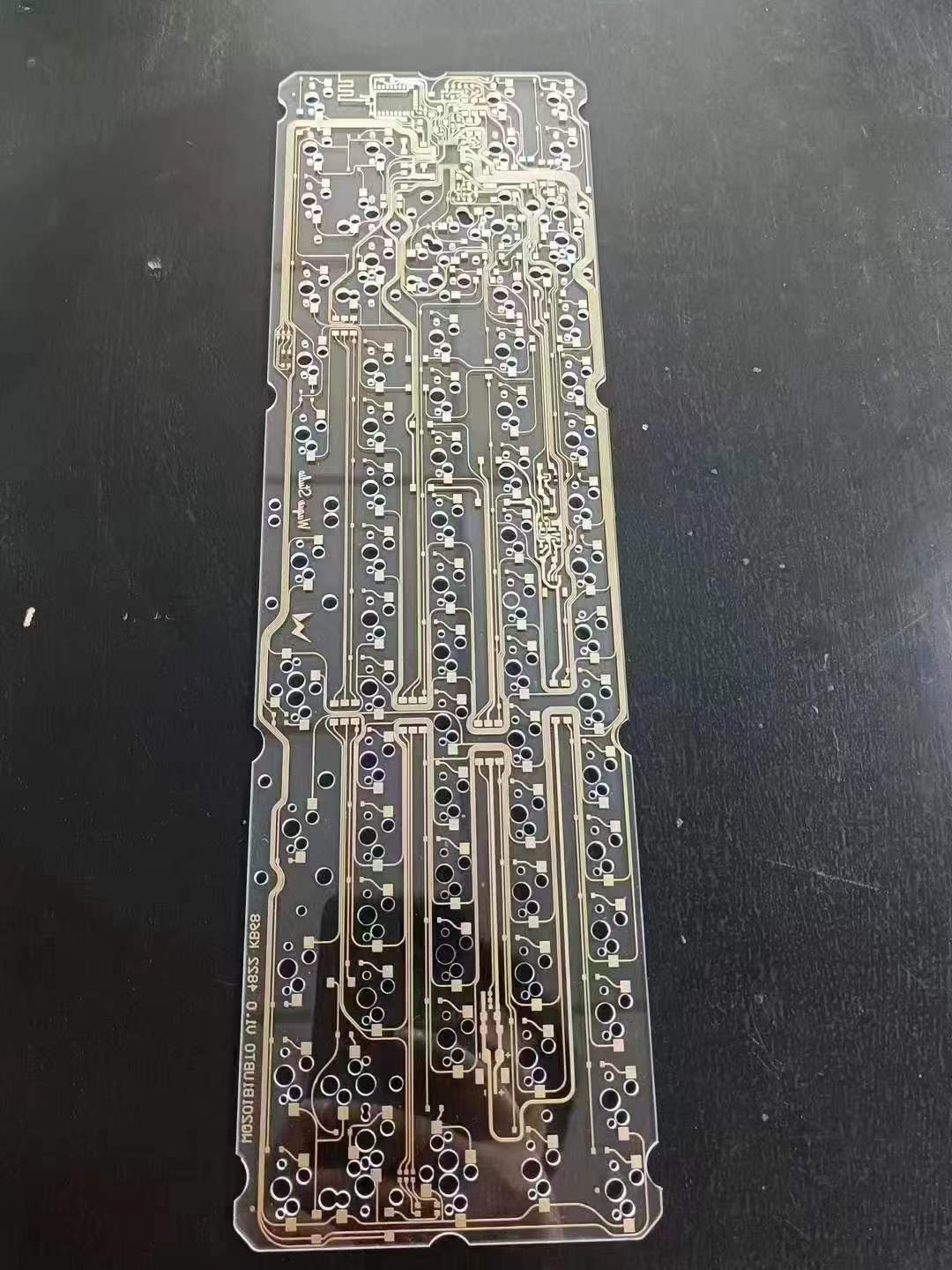
Previous